How we save our customers 10-20% on operational costs
› Ventilex is a world leader in the minerals market, with an installed base of over 1,000 machines
› Many customers focus on initial equipment price but do not think about the operational costs
› Regular service and technical advice are a must for production reliability and lower operational costs
› Ventilex offers solutions to reduce operational costs and unscheduled downtime by 10-20%
› Our global team of service experts is ready to help
Our established place in the market
Established in 1965, Ventilex has since grown to become a global leader in drying and thermal treatment equipment. Our fluid bed dryers, sterilizers, belt dryers and air dehumidifiers serve customers nowadays in more than 80 countries.
We have an installed base of over 1,000 machines, nearly 50% of which are in the minerals market. We have grand experience in the thermal treatment of sands, salts and processed mineral products. Our technological expertise includes drying of minerals according to custom designed thermodynamic profiles, covering the drying, cooling, calcination, roasting, puffing and sterilization of mineral products. In addition, we possess deep knowledge of energy-saving and heat-reusage techniques that help our customers reduce operational cost per ton produced.
Customers in the minerals market often face high operational costs and downtime
The mining, processing and treatment of minerals makes up for a harsh environment:
- Equipment is exposed to strong, dynamic forces
- Processing involves heavy mechanical and chemical abrasion
- Processing temperatures are high, accelerating wear and tear
- On-site personnel often lack skills on how to operate the equipment
- Equipment operation is often not monitored (data log) to analyze improvement potential
Adding all this up means a much higher than average risk for unscheduled downtime, equipment failure and lacking product quality – if proper action is not taken. Surprisingly, many customers in the minerals market focus on the initial equipment purchasing price, but forget to think about lower operational costs during operation afterwards.
Reducing your operational costs with our service and technical advice
We provide a whole package, consisting of:
- Inspection: regular inspection to identify possible maintenance needs before unscheduled downtime occurs
- Maintenance: regular cleaning, refurbishing and replacement of critical equipment parts
- Spare parts: stock of critical spare parts on-site, ready to deploy in case of repairs
- Certification: periodic burner inspection and safety certification
- Optimization: quarterly operational improvement feedback based on equipment data (data log), leading to actions to optimize your operational settings
- Training: regular training of personnel to ensure proper use of equipment, based on usage data
This total service package ensures problem-free operation and a long lifetime. Our data shows that compromises made on any of the above factors rapidly reduce lifetime and increase the operational costs. Problems that you would most likely want to avoid.
The impact: saving 10-20% on your operational costs
Ventilex’s professional service and advice package leads to tangible, direct savings on your operational costs, along with improvement in your operation’s continuity and product quality:
- Insights: operational reports before periodic inspection/maintenance provide you with valuable insights and opportunities to reduce cost and improve quality, based on actual equipment usage data
- Extended warranty: machines within our service benefit from 24 months – instead of 12 months – warranty
- Near zero downtime: equipment without regular, professional servicing typically has an unexpected downtime of 5-10% of operational hours. With a service agreement, this is reduced to nearly zero, allowing you to run continuously without problems, saving large amounts of downtime costs
- Operational cost savings: professional service and operational advice save customers 5-10% of operational cost in reduced down time, energy use and improved quality
- Stable quality: predictable product quality based on fine-tuned operational settings
Our team is ready to help
We have a team of 20 skilled professionals who provide quality service around the world, each and every day. We have great experience in dealing with the challenges that customers face in the harsh environment of the minerals business. We are here to help you reduce operational costs, reduce unscheduled downtime and increase quality.
Are you struggling with your current machinery or looking for a suitable solution to your drying needs? We welcome you to contact our experts.
Require Service?
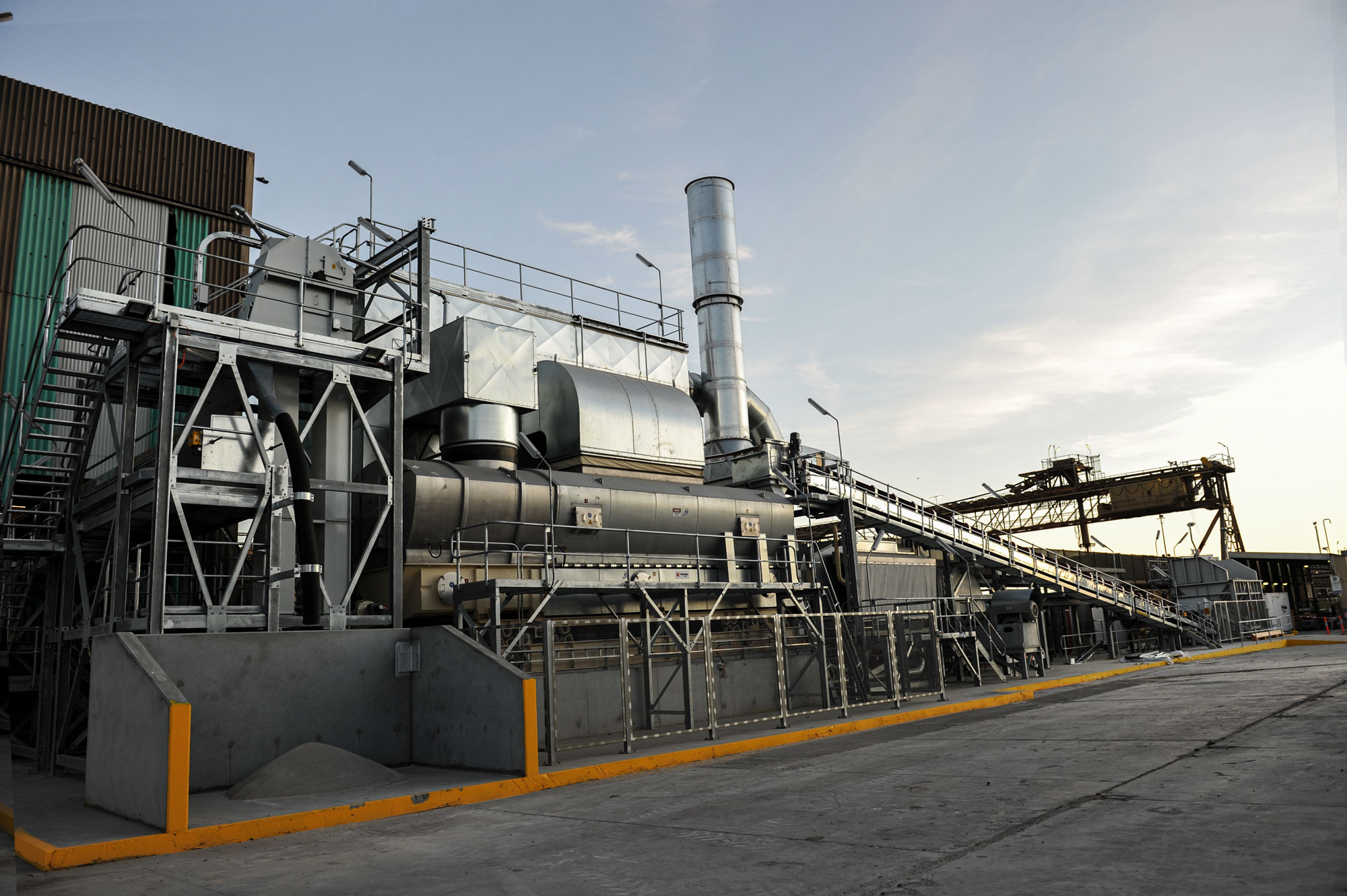